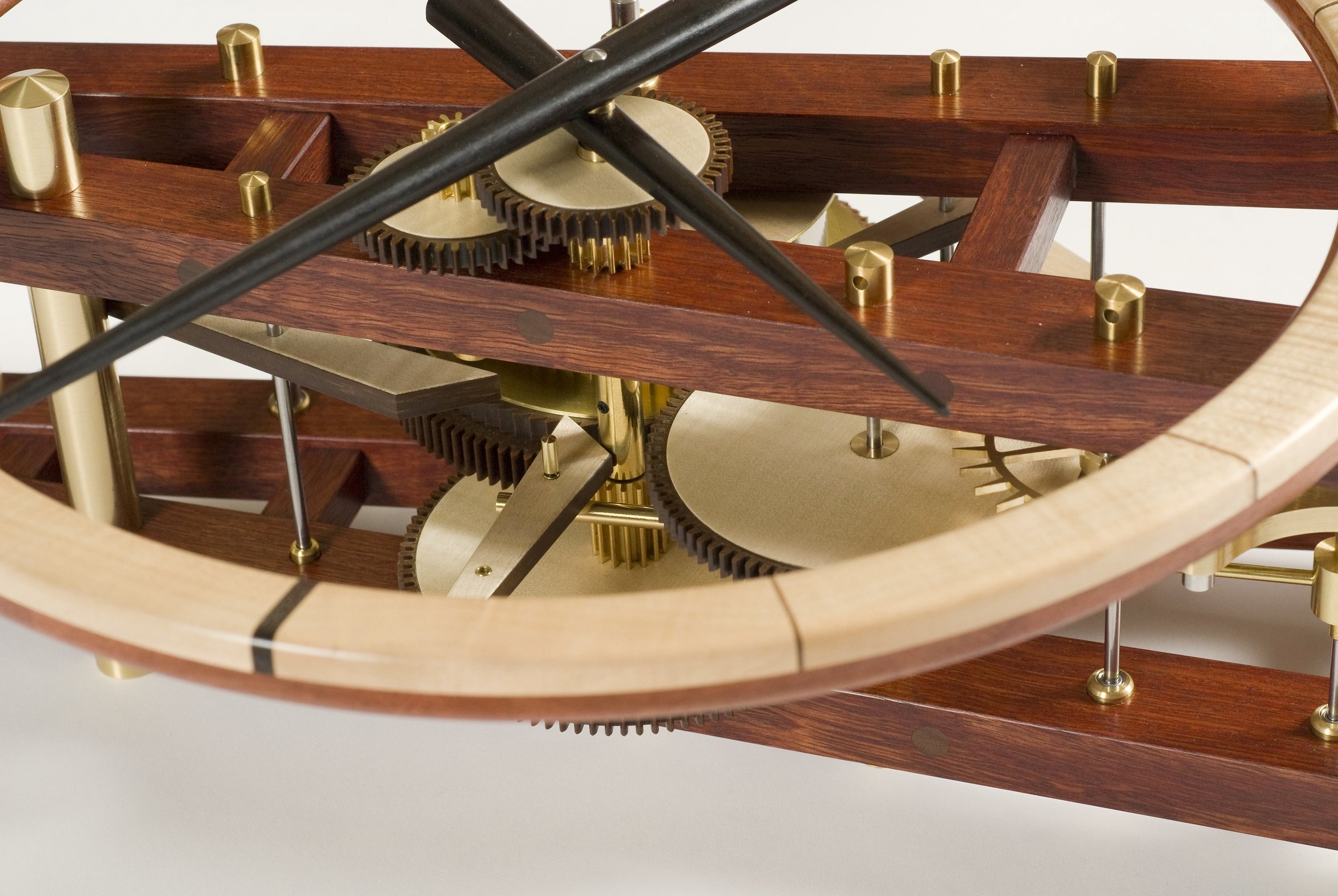
Technique
Will Matthysen is a designer and maker of handcrafted custom clocks and furniture.
He works full-time from his workshop in Warrandyte, Victoria, Australia.
The Design
Will Matthysen is responsible for the design, prototyping, detailing and production of all his clocks. Numerous concept sketches are made for each clock, generally small three-dimensional views, followed by scaled technical drawings enabling him to visualise the whole object. The scaled working drawings are done to resolve every detail. Will does not regard a working drawing as the final stage in design, but as part of an ongoing process which only ends when the piece is completed. Wood as a natural material is incorporated into the overall design, and should also be allowed the freedom of influencing it.
When developing a totally new design, Will constructs a working prototype. This enables him to see the piece in the round, to fine tune the workings of the mechanism, and see how the shadows fall once illuminated by artificial lighting. It is here that he makes any final changes before commencing production.
Several designs have evolved over the past 20 years, including both weight and spring driven clocks. The clocks and cabinets often refer to architectural forms and shapes. Broadly speaking, they can be arranged into three types:
Free-form sculptural pieces, can be representational, wall mounted, size varies.
Long-case clocks, in wall mounted cabinet, sizes from 1.0m to 1.8m high by 0.4m to 0.6m wide.
Mantel clocks, in free standing cabinet, sizes from 1.1m to 0.6m high by 0.4 to 0.5m wide.
All clock movements can be fitted with complications such as strike mechanism and lunar dial.
Computer Aided Design (CAD)
In recent times, the use of Computer Aided Design (CAD) software has been employed to help establish scale, composition, and precise component spacing. It also allows for the creation of high-quality photorealistic renders of the desired outcome, which helps to inform wood selection while illustrating the design direction of commissioned pieces well before the making process has commenced.
CAD Photorealistic Render
Clock 186 - Photograph
CAD Photorealistic Render
Clock 199 - Photograph
Workshop and Equipment
Will Matthysen employs both traditional hand craft techniques, as well as computer numeric controlled (CNC) equipment to produce his clocks. This enables him to combine woodworking skills which celebrate the quality of the material, as well as the intricate mechanisms and precision engineering associated with clocks. Depending on the nature of the project, the various components of the clock movement and clock case are made from brass and steel, wood or composite material.
The Making
Success depends on a sound and well thought out design, appropriate material selection, sensible detailing and construction, and a manufacturing process which produce the components to the desired tolerance and finish.
All the clocks are fitted with the Harrison type maintaining power, which ensures the clock keeps running during winding. The accuracy of the clocks is in the order of 10 seconds a day. This accuracy is dependent on a number of factors, such as the type of escapement mechanism used, the consistency of the power source, the design and stability of the pendulum and bob, and the overall smooth operation of the wheel train.
Most of Will’s clocks employ the Brocot dead beat escapement, as it provides easy adjustment and trouble free operation. He has also produced other clocks using the Harrison Grasshopper escapement. Will's clocks are either weight or spring driven, giving an 8 day running period.
The Use of Wood
Great care is taken in the selection and seasoning of the wood. Quarter sawn wood is inherently more stable than back sawn material, and hence is preferred for use. Where the wheels are made of wood, the wood is cut into segments and then glued to form a ring where the grain runs parallel to the tooth of the wheel, giving it maximum strength. The wheels and pinions are mounted on steel arbors, and the pivots run in stainless steel and ceramic micro ball races to minimize friction. The entire clock movement can be dissembled for future service of repair, and is fully adjustable.
The timber drying and seasoning procedure is extremely critical. The process here is to pre-dry the material to a moisture content well below that of the environment that the clock is likely to be used. Will re-saws his air-dried timber into the approximate sizes of the various components, and then places them in a heated drying cabinet for a number of weeks to bring the Equilibrium Moisture Content (EMC) to around 7% to 8%, and then removing them from the cabinet and letting them reabsorb moisture to workshop conditions, and preferably repeating this process a few times, before further machining and assembly. The wood will now have an EMC below that which it would normally have if it was losing moisture. This is known as the hysteresis effect, which minimizes the subsequent expansion or shrinkage in future, making the wood more stable.
Will is interested in finding relatively obscure Australian species that are suitable for use in clockwork. In particular, some of the Outback desert Acacia species are extremely slow growing, dense and stable, and are suitable for a variety of mechanical applications, such as wheels and pinions. These wood species include:
Gidgee (Acacia cambagei)
Mulga (Acacia aneura)
Myall (Acacia pendula)
Leopard wood (Flindersia maculosa)
Belah (Casuarina cristata)
The clock plates and the rest of the clock cabinet can be sourced from a broader variety of Australian timbers, with the selection based not only on mechanical properties, but also on aesthetic considerations.
Jarrah (Eucalyptus marginata)
Redgum (Eucalyptus camaldulensis)
Red Box (Eucalyptus polyanthemos)
Red Stringybark (Eucalyptus macrorhyncha)
Red Ironbark (Eucalyptus crebra) Mountain Ash (Eucalyptus regnans)
Huon Pine (Lagarostrobus franklinii)
Black heart Sassafras (Atherosperma moschatum)
Myrtle Beech (Northofagus cunninghamii)
Blackwood (Acacia melanoxylon)
Testing
After completion, the clock movements are mounted on a test stand or wall. The Microset Timer is set–up with an infra-red sensor to time the period of the pendulum. Initially the clocks are brought to run on time; then the data is fed into a computer which analyses it over a period of weeks. The resultant graphic data can now be used to detect where the clock needs further adjustment.